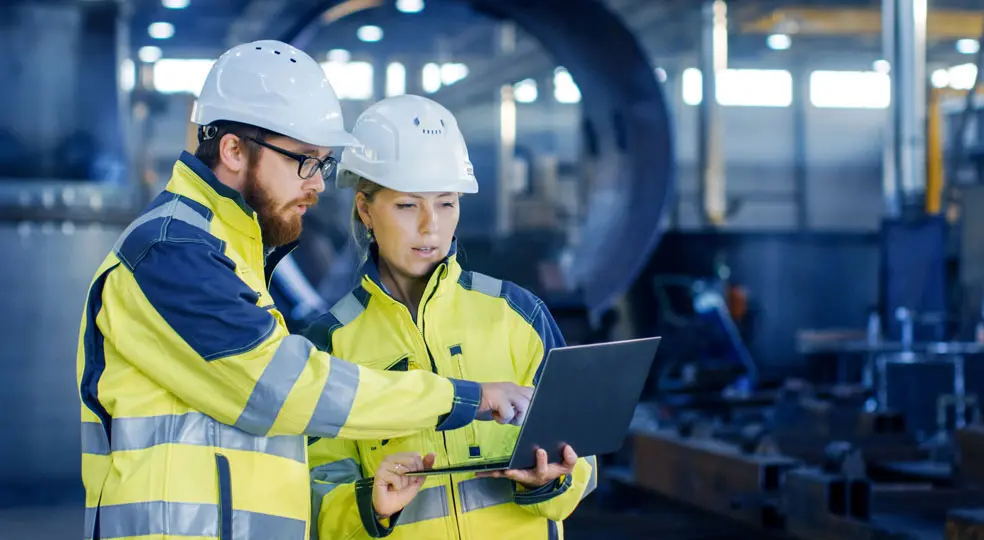
EMPLOYEE ENGAGEMENT: THE SECRET TO A SAFE, PRODUCTIVE ENVIRONMENT
INTRODUCTION
Customers have developed high expectations, and the pressure for manufacturers to reduce production time is high. At the same time, you must maintain the quality of your output, as customers won’t accept lower quality.1And then there’s safety. Safety incidents stall production and lead to spiraling costs on and off the production floor.What’s the root cause of these issues, and how can you remedy them? The reality is, engaged employees are more productive and less likely to have a safety incident.2 But to reap these benefits, it takes proactive efforts to foster employee engagement.
SPOTLIGHT ON SAFETY
Manufacturers have made significant progress in the last 25 years to reduce safety incidents, and the data reflects that.3 But there’s still a long way to go. According to the National Safety Council, manufacturing is one of the top occupations where employees experience the most injuries resulting in days away from work, ranking behind public service and transportation and shipping.4
The True Cost of a Safety Incident When an accident happens, the effects aren’t just limited to the factory floor. Beyond the direct costs associated with worker’s compensation and insurance, there are numerous indirect costs. Indirect costs can include hiring and training replacement employees, lost productivity, repairs to damaged equipment, accident investigation, and lower employee morale. Insurance doesn’t cover these costs, so your company has to absorb them. If a company has a 5% profit margin, it will need $11 million in new sales to make up for just eight strain injuries.
Estimated total of employers’ uninsured costs incurred due to worker injury in 2018.6 - UP TO 12.8 BILLION
The Cost of Poor Quality
For some manufacturers, quality issues can be captured before the product leaves the production floor. For others, many quality issues aren’t realized until the product has gone to market, resulting in costly recalls.The cost of poor quality accounts for 10-15% of operations, according to the American Society for Quality.7 This metric is calculated based on appraisal costs, internal failure costs (such as waste and reworking), and external failure costs(such as returns and complaints handling).When combined with the cost of safety incidents, manufacturers need a proactive way to tackle these revenue-eating issues
Manufacturing is #3among industries with the highest number of workplace injuries.5
WHAT CAN BE DONE – BETTER EMPLOYEE ENGAGEMENT
Stronger safety standards and process improvements have improved production quality and safety over the last 25 years8. But there’s one area that hasn’t received much attention, and it threatens to undo some of the progress that’s been made: employee engagement.
Employee engagement is a serious problem in the United States, and manufacturing lags furthest behind.Gallup says that a failure to keep up with trends that other sectors have made advances in is the reason behind the trend. Whereas flexible work schedules and deeper engagement with day-to-day decision-making are becoming more common in other sectors, manufacturing employees don’t enjoy those perks.
The Correlation Between Engagement, Quality, and Safety Engaged employees perform better – both in terms of safety and quality. Companies with high rates of employee engagement report 48%fewer safety incidents and 41% fewer quality incidents, according to the HarvardBusiness Review.All of the perks that non-manufacturing employees enjoy may not be possible in manufacturing environments. But that doesn’t mean that employees should accept the nearly 100-year-old model that many manufacturing employees work under.
CONCLUSION
As the numbers show, manufacturers need to take employee engagement seriously. Otherwise, you risk undoing some of the progress that’s been made in improving employee safety and undermining your efforts to improve product quality and production speed.While identifying ways to streamline your operations through outsourcing, seek out partners who understand the correlation between employee engagement and production quality and safety. The data on costs show it’s worth the effort.
Sources:
1. https://engagedly.com/impact-of-employee-engagement-on-productivity/
2. https://hbr.org/2013/07/employee-engagement-does-more
3. https://www.bls.gov/spotlight/2019/25-years-of-worker-injury-illness-and-fatality-case-data/pdf/25-years-of-worker-injury-illness-and-fatality-case-data.pdf
4. https://www.nsc.org/work-safety/tools-resources/infographics/workplace-injuries
5. https://www.nsc.org/work-safety/tools-resources/infographics/workplace-injuries
6. (includes time spent investigating and reporting injuries, administering first aid, hiring and training replacement workers, and the extra cost of overtime for uninjured workers) https://injuryfacts.nsc.org/work/costs/work-injury-costs/
7. https://asq.org/quality-resources/cost-of-quality
8. http://www.bls.gov/spotlight/2019/25-years-of-worker-injury-illness-and-fatality-case-data/pdf/25-years-of-worker-injury-illness-and-fatality-case-data.pdf