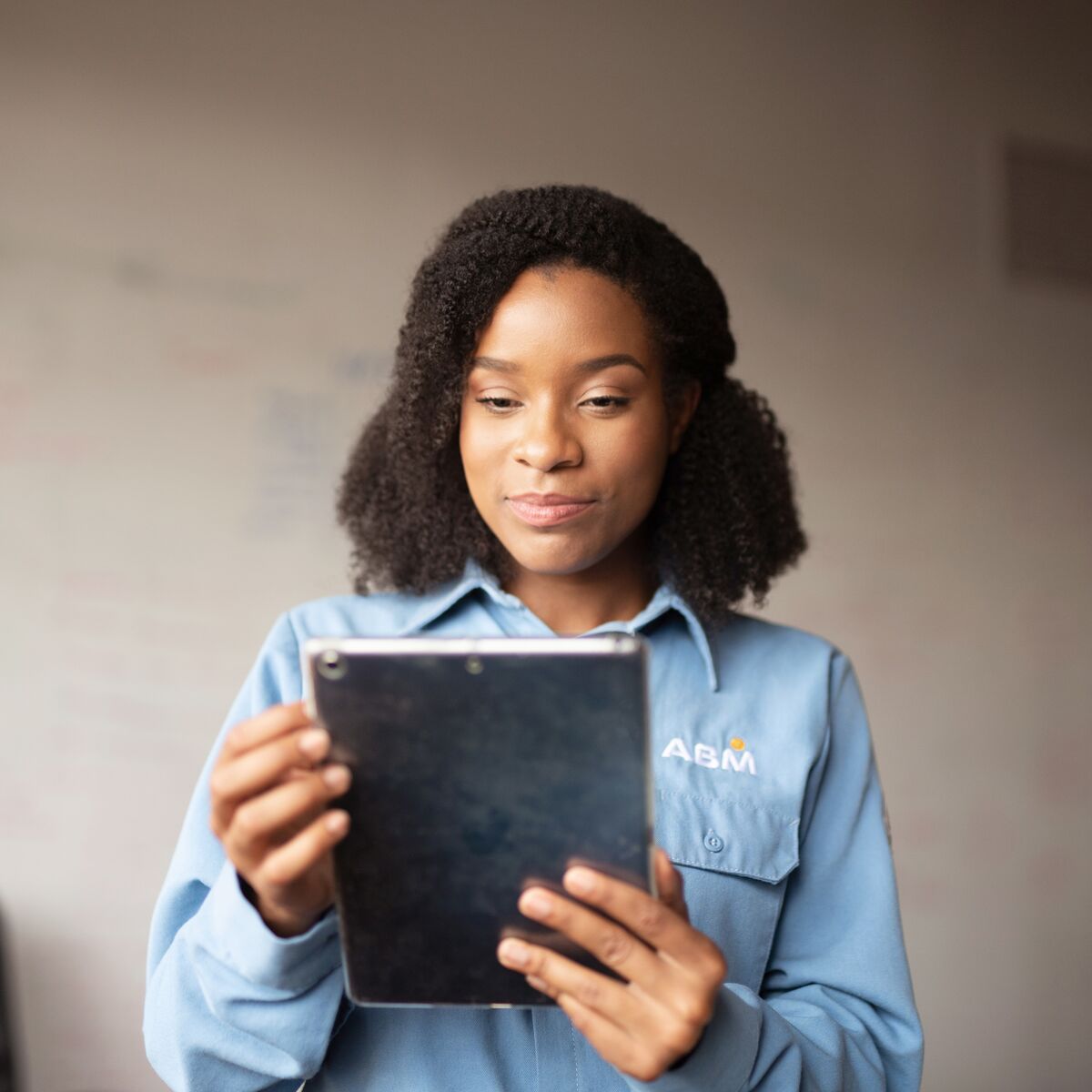
5 MAINTENANCE SCENARIOS
PROACTIVE VS. REACTIVE
Nothing lasts forever, including facility systems and equipment. The length and quality of its lifecycle depends on the care it receives. And in your facility, systems can be cared for in one of two ways: through proactive maintenance to prevent or minimize potential disasters or reactive maintenance after the dust settles. Check out these scenarios that explore how each approach might play out.
1 SCENARIO
Fall has settled in and the first cold day of the year is here. It’s time to turn the heat on. But soon afterflipping the switch, a burning odor fills the air — and then the heat stops flowing entirely.
REACTIVE
Your facility’s heating worked perfectly fine last season. But after being out of commission for so long, it’s no surprise that dust built up and is now being burnt off. But if the machine accumulated too much buildup, it might be a lost cause. You’ll have to troubleshoot the problem, spending unwanted dollars and time on replacing air filters, servicing the thermostat, and if that didn’t solve it, tracking down a power issue. If nothing works, the machine might need to be replaced entirely.
PROACTIVE
During the warmer months when your heating system is out of use, it’s important to regularly maintain it. With so much on your plate as is, you can call upon your dedicated engineering partner to tackle the job for you. They’ll regularly clean your air ducts and replace filters. With a cleaner system, you’ll have better indoor air quality (IAQ) and more efficient circulated heating, meaning lower energy bills, too. And when winter finally returns, you’ll be able to flip that switch with confidence.
2 SCENARIO
A bathroom sink has occasionally been spouting discolored water, a sign of potential pipe corrosion.By the time you notice pinhole leaks on another pipe, the original pipe has completely burst.
REACTIVE
A burst water pipe under the sink might be a nuisance, but a burst pipe behind your walls can be a serious problem. Water leaking into ceilings, walls, or across floors of your building can cause extensive damage to your drywall, insulation, and wiring, meaning you’ll need more than a bucket and mop to clean this mess.
PROACTIVE
Routine inspection of your pipes is a must to curb any unforeseen disasters. If minimal damage is found, it’s best to replace your pipes as soon as possible. If a larger replacement project is necessary, you can leverage your engineering team to safely shut off the water flow and replace internal pipes. You can go further to save on your water bill with automated water meter systems, ensuring accurate water usage billing.
3 SCENARIO
A lock on a rear entrance door to your facility has been loose for some time, but unnoticed by you and your team. One morning, you enter the office to find the unimaginable: your computer equipment, office supplies, and more have been stolen.
REACTIVE
The first step would be to safeguard your facility by replacing your locks and ensuring all entrances are secure. If brute force was used onthe unsecured lock, you might have to replace the door, as well, and would be highly motivated to look into a stronger security system altogether. That’s not even mentioning the stolen equipment, police reports, replacement purchases, lost productivity, insurance claims, and more.
PROACTIVE
Routine inspection means taking note of your facility from the outside, as well. Onsite engineers should regularly check your site for vulnerabilities, including locks on doors and garages. If any locks are showing signs of wear and tear, especially outdoor locks in areas of severe weather, it might be time to replace them. For added convenience, look for an engineering team that offers locksmith services to streamline the workload.
4 SCENARIO
Your facility’s electrical wiring has been operating fine for years, but your infrastructure is reaching the end of its life. After a bad storm, your power system finally fails for good.
REACTIVE
If you don’t have backup generators ready to go, replacing your entire source of power will leave your facility practically inoperable for days to weeks at a time. Depending on the condition of your electrical system prior, you might have been unknowingly out of compliance and might now be facing a number of fees for the error. What’s worse, unsafe electrical conditions could spark a fire, meaning destruction that results in more than a loss to your operating budget.
PROACTIVE
Keeping a proper maintenance schedule is key to knowing when and where your facility needs attention. You can test your building’s electrical efficiency by checking for flickering lights, repeatedly tripped breakers, a noticeable burning smell in some rooms, and signs that an appliance isn’t properly grounded. For bigger jobs, turn to your engineering partner to properly test all of your systems. They’ll know how to keep your facility compliant and keep your occupants safe.
5 SCENARIO
Your facility is growing — and so are its engineering needs. The dedicated rooms for your facility’s missioncritical needs must be temperature regulated to ensure a stable environment. But the same air conditioning system used in the rest of the building is no longer cutting it. As your processing power expands, so does the heat, and your unprepared HVAC leads to a critical failure.
REACTIVE
You need an HVAC upgrade stat. While your operational power and your business takes a backseat, you’ll be forced to find the right replacement fast, likely jumping at the best deal possible on a mission critical cooling system. Only once your system is operational again will you be able to analyze the performance of what you bought.
PROACTIVE
Keeping a proper maintenance schedule is key to knowing when and where your facility needs attention. You can test your building’s electrical efficiency by checking for flickering lights, repeatedly tripped breakers, a noticeable burning smell in some rooms, and signs that an appliance isn’t properly grounded. For bigger jobs, turn to your engineering partner to properly test all of your systems. They’ll know how to keep your facility compliant and keep your occupants safe.
Which is Best for Your Facility?
Some teams consciously choose to operate a Run To Failure (RTF) system of maintenance. For lightbulbs and fuses, that might make sense. But for facilities that can’t afford downtime, proactive maintenance can make all the difference: an estimated 10–40% reduction in costs and nearly 50% reduction in downtime when compared to reactive maintenance. 1
Anticipating future problems through proactive maintenance is more likely to save you money in the long term.Taking the time to carefully consider your facility needs and conduct the proper analysis on each system is key to making that call. The guidance of a professional engineering partner can help.
SOURCES:
1. Reactive Maintenance vs. Proactive Maintenance: You’re Paying 2-5X More for Maintenance. https://www.omega.com/en-us/resources/proactive-maintenance-vs-reactive-maintenance